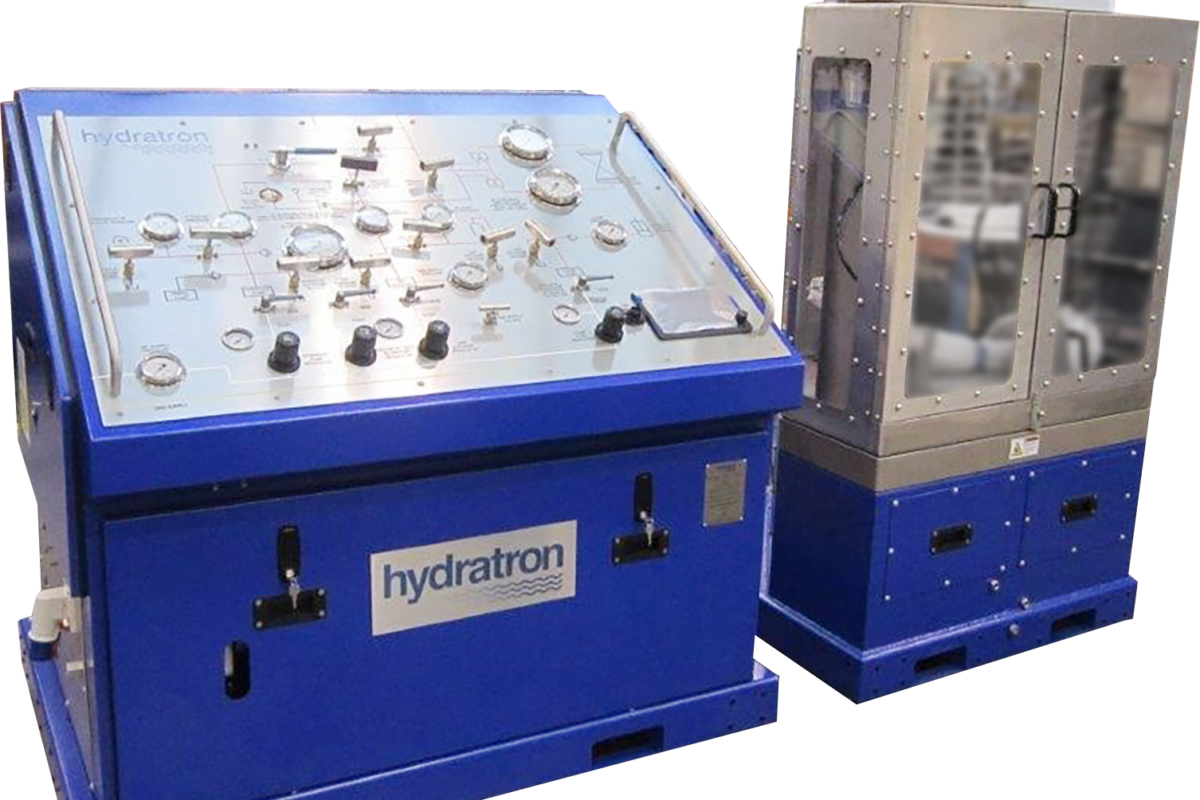
Large, UK-based valve manufacture, Colson X-Cel contacted Hydratron to provide a valve test solution capable of testing their wide variety of process valves during production. The diverse range of valves to be tested varied in size from 1/2″ to 12″ and would need to be tested using both liquid and gas test mediums with pressures up to 10,000 PSI.
Process Valve Testing Requirements
Colson X-Cel needed to be able to carry out both body and seat tests on all valves going through production.
Due to the high pressures involved in the testing, a fully enclosed test compartment would need to be designed on the unit. The clamping arrangement for holding the valve under test and the control console would be on separate skids to allow Colson X-Cel to test in a separate enclosure for additional safety.
As part of the valve production process, Colson X-Cel wanted a way to record and store valve test results so that valve test certificates could be made for each valve.
Key Features
- Engineered to fit a wide range of valves
- Valve testing with multiple methods:
including- Upstream valve testing
- Downstream valve testing
- Valve body testing
- Separate control and test areas
- Off-bench testing capability
- Automatic clamping pressure calculation
- Vertical valve clamping arrangement
Engineering the process valve test system
Our engineers engaged directly with Colson X-Cel to review the requirements in detail. Working in collaboration with our clients ensures that we have a full understanding of the requirements.
One of the challenges was ensuring that the clamping system was capable of securing the large of range of Colson X-Cel valves for testing. An off-bench testing system was included in the design to allow for the testing of larger valves.
After extensive design work, Hydratron were able to present a complete valve testing solution to Colson X-Cel which enabled them to meet all their testing requirements and more. Our universal valve test unit not only allowed for testing of process valves, but also allowed for testing of relief valves would this ever be required.
Our design incorporated a PLC and HMI to automatically calculate the clamping force required for the valve to be tested by entering the valve size and test pressure. This reduced the possibility of incorrect clamping force which could damage the test piece or prevent a sufficient seal. The PLC also provided the user the options for body or seat testing of the valve ; this automatically actuate the required valves in the system to route the test pressure in the required direction.
Clamping valves securely during testing
The valve clamping arrangement was designed to prevent any clamping force getting transferred to the valve body. This prevents additional stress on the bolted joints, and ensuring correct valve testing. The valve clamp was designed in a vertical orientation enabling the user to easily purge air out of the valve prior to testing. Time taken to prefill the valve was reduced to a minimum with the use of a high-volume, low-pressure, electric-driven centrifugal pump incorporated into the system. Low-pressure purges fluid from of the valve post-test.
Flexible valve testing solution
The control console and clamping arrangement were manufactured on two different skids which connected by hoses to allow for Colson X-Cel to test valves in a dedicated valve test area. Since the original requirement, Colson X-Cel have moved site and are not only using the rig as designed to test numerous process valves, but is now also being used in a slightly different way to enable them to carry out gas under water testing of valves. By designing an building the valve clamp table on a separate skid, Colson X-Cel can use the control console independently to perform this testing.
About Colson X-Cel
Colson X-Cel Ltd was established in 1995 to manufacture a range of instrument ball, needle, check, manifold and Double Block and Bleed Valves. Colson X-Cel Ltd are approved by major oil and gas operators such as BP, Shell, Qatar Petroleum and North Oil Company with a global track record in the oil and gas industry. In 2020 Colson moved to a brand new state of the art facility at the Advanced Manufacturing Park just outside Sheffield. Colson design, machine, assemble, test and QA in house to ensure operational excellence.