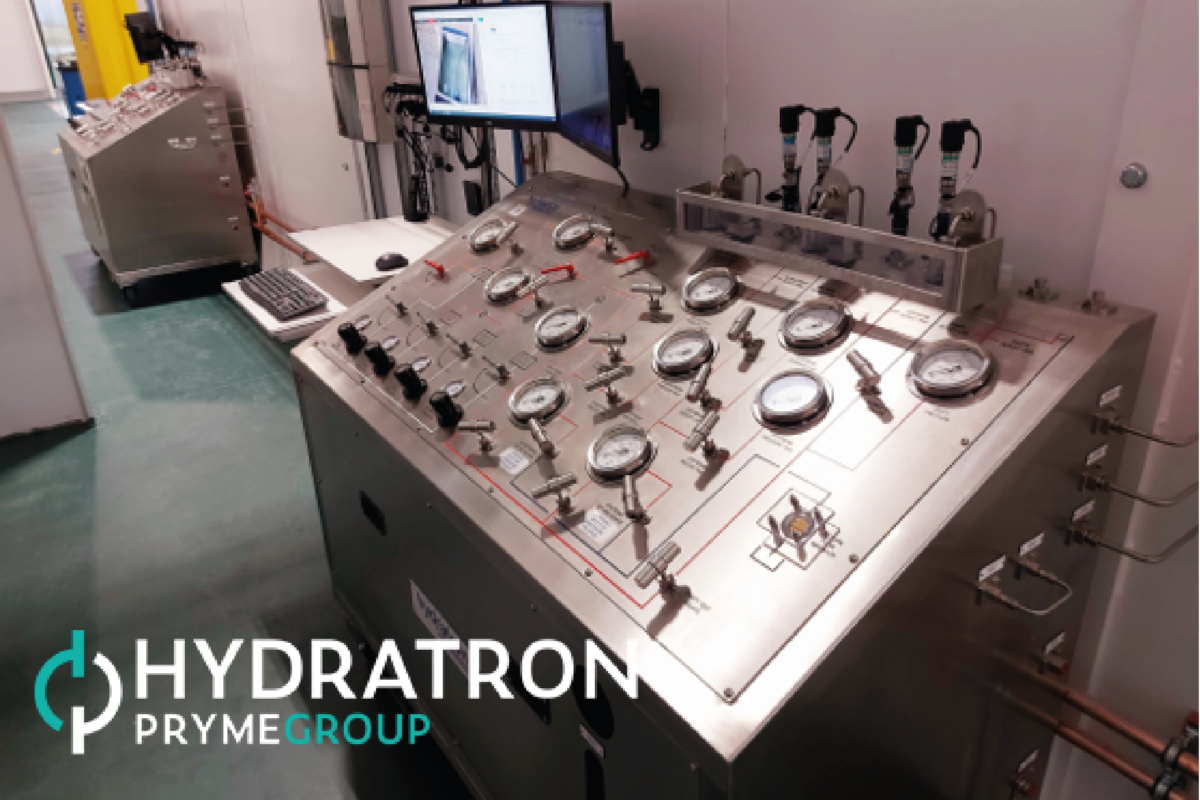
We were recently approached by a UK-based valve integrity management and servicing company to assist them with the Global expansion of their service offering to clients in the: O&G, Refining, LNG, Marine, Energy, Mining and Paper industries. Our client had a requirement to expand their valve asset management offering and contacted Hydratron to assist with the design and manufacture of a new ‘twin-cell flexible test system’.
Our Approach
We entered into a collaborative partnership with our client and were appointed the supplier of choice for pressure testing equipment for the new facility. Having always been hailed for our expertise and attention to detail, our technical sales team soon set to work establishing a firm understanding of what was required. We reviewed the entire scope of supply to quickly determine where we could best add value to the project and advise which elements they would be best sourcing elsewhere.
The Solution
The client was looking for a fully flexible 2-station test set-up for high and low-pressure testing with liquid and gas, enabling them to pressure test on the upstream and downstream sides of a wide range of valve products across all sectors. This is a key part of Hydratron’s collaborative approach, understanding our clients’ requirements and designing the correct system to provide the client with the best possible outcome.
Whilst complex, the technical requirements of the rigs were well within Hydratron’s capabilities. Each system has 3-off independent twin outlets/returns all of which were served by a combination of:
- Low pressure pump liquid providing up to 1200psi,
- High pressure liquid pump providing up to 23,700psi
- 2-stage gas booster providing up to 15,000psi
Each line was linked to an air blowdown to facilitate switching between mediums and each of the 3-off outlet/return were also fitted with a bubble pot for gas leak testing. Our client already had a data acquisition system in place and so each system was also configured to provide pressure transducers on each of its six outlets to tie into the data acquisition equipment.
With a number of configuration iterations throughout the design and build, by collaborating with the customer and paying close attention to their requirements we were able to deliver a system that is exactly what they wanted. Following successful factory acceptance testing the customer took delivery and integrated the systems into their new facility and having done a fantastic job with the installation we think their set-up looks beautiful.