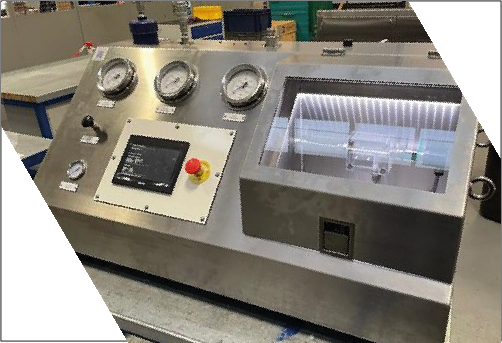
Requirement
A leading manufacturer in the Aerospace industry approached Hydratron to design and manufacture a specialist valve test bench. The unit was required to test a special valve which operated by releasing pressure within a specific pressure band and needed to hold pressure both below and above the releasing pressure range.
The customer had been using a very old and completely manual test system which was taking an excessive amount of time to test the valves and due to the manual nature of the testing, consistency needed to improve. The new system would also address some general health and safety concerns posed by the manual test system.
Initial Action
Our Systems Engineer attended the customers site to carry out an inspection of the existing unit, gain an understanding of the issues with it and review the test procedures. There were two particular tests required, which were being completed on two separate sections of the test unit; a proof test to 25 Bar and then the functional test ranging from 0.37/0.4 Bar to 2.2 Bar.
Challenges / Solution
The test procedure for this particular valve was complex; the functional test required the system to bring the pressure to a point, hold and ensure the valve is not releasing. It then needed to take the pressure to a point in the mid range of the releasing pressure band, releasing of liquid then needed to be observed. Next, the pressure needed brought up to the valve closing pressure, check that no liquid is releasing and that the valve had closed again and then this needed to be repeated with the same logic in reverse, reducing the pressure back down again.
The pressure needed to be measured in Bar(G) and accuracy was required to two decimal places with the lowest pressure required to be holding within a tolerance of 0.37 – 0.40 bar. The full test sequence in relation to pressure ramping was to be fully automated with pause points to allow operators complete the required visual checks.
Pressure ramping needed to be slow and smooth, which presented a challenge due to the lack of volume in the test valve itself coupled with the fact that liquid was the required test medium, we over came this by designing an air over liquid system which provided extremely smooth and accurate pressure control.
It was also a requirement for the manifold block – which the valve undergoing test would be fixed to inside the main interlocked test complement – was clear to allow operators visually see the liquid entering and leaving the valve. The full system needed need to be compact and designed in such a way so it could be mounted on an existing work station table.