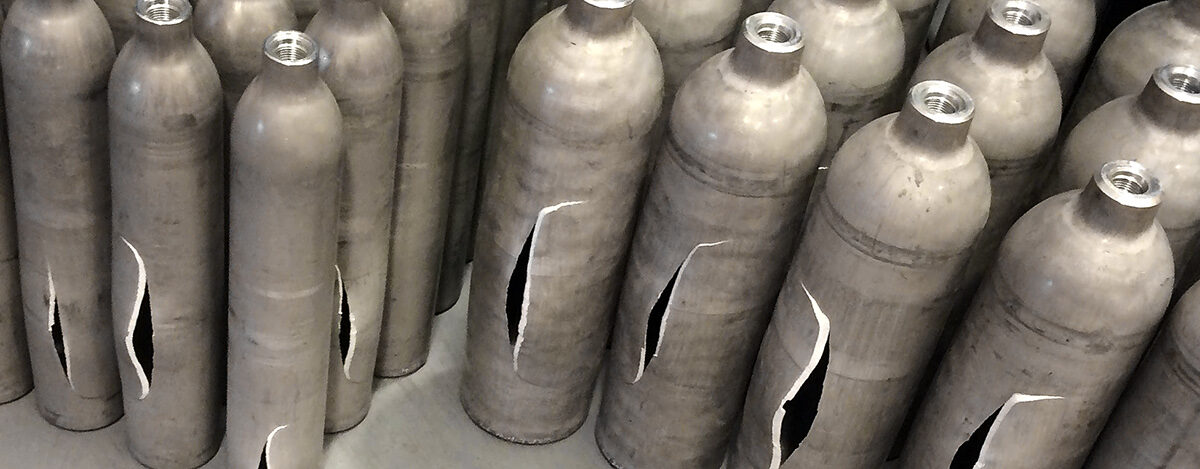
A global manufacturer operating in the food and drink industry approached Hydratron with a demanding requirement to take on the design and manufacture of a production type pressure cylinder burst test rig rated to a maximum working pressure of 1000 Bar.
Burst test requirements
The client needed to burst a rolling sample of their total production of pressure cylinders as part of the manufacturing standards they needed to adhere to. This translated to a maximum allowable test time (including loading and removing) of 6 minutes. The burst test machine needed to be simple to setup, reliable and robust enough to run continuously, 24 hours a day, 7 days a week. As part of the workflow, Full data logging of all test results needed to be recorded and exported directly to the client’s network.
The test standard also required detection graphically and numerically of the yield point of each cylinder prior to failure.
Two modes of operation were required for the burst test rig:
- Fully manual burst testing – Where the client has the capacity to carry out testing on non-standard items and to prove testing before automated production runs.
- Fully automatic burst testing – for standard product testing.
Key Features
- Designed for continuous, 24/7 operation
- Graphical and numerical recording of cylinder yield point
- Visual pre-fill indicator
- Fast testing times (under 6 minutes)
- Built to withstand shock forces
Understanding critical requirements
Hydratron allocated the project to one of our System Engineers, who then engaged with the client’s engineers to form a direct person to person line of communication between the two companies. This ensured that all requirements were picked up, understood, and addressed in the most efficient way. All test requirements and details of the cylinders were obtained and reviewed by the Hydratron design team. By visiting the customers facility overseas we were able to better understand their critical requirements.
Test Rig Design Challenges
By working closely with the client, we were able to identify the main design challenges as follows.
Prefilling the test component
All of the air needed to be fully expelled from the cylinder prior to pressurisation. A way was needed for the operator to be able to visually verify this and there was only one connection located at the top of the cylinder to both prefill and pressurise. Our engineers designed a special test connector which allowed air out from the cylinder when prefilling. This air release port was connected back to the fluid supply tank via a fluid indicator mounted on the control panel. In doing so this provided the operator with a visual indication of when all the air had been removed from the cylinder being tested and was safe to pressurise.
Ensuring test times are achieved
This was estimated by first using the internal volume of the cylinder and sizing a low pressure prefill pump to obtain the optimum prefill time. Using the bulk modulus for the test fluid, the volume to be introduced to the prefilled cylinder to bring the internal pressure to 1000 Bar was calculated. From here they were able to select a suitable Hydratron pump for this and determine full cycle times.
Withstanding repeated shock forces
The repeated shock forces created by the cylinders bursting needed to be carefully considered. The burst test rig would be in continuous 24/7 operation and the shock forces would be a challenge throughout the test lines; Integrity of the pressure line and fittings needed to be maintained. Testing was carried out at the Hydratron facility on various types of high-pressure connections and fittings. Standard connections were found to loosen after a short period of testing and subsequently began to leak. Continued testing and research lead to the selection special fittings which, when put under test, were found to give the required repeatability and so were incorporated into the burst test rig design.
Recording the material yield point in burst testing
Special software was written into the PLC Control and data logging system to monitor the pressure ramp rate and identify when the cylinder begins to stretch prior to bursting. From this the software had the ability to calculate the material yield point. This information was then plotted onto the test graph and numerically displayed on the test report.
Burst testing rig – designing the solution
A detailed technical proposal and specification was issued to the client, who on review, instructed Hydratron to proceed. A full internal contract review was completed by Hydratron systems engineers, design engineers, production and procurement teams.
The detailed design was completed and submitted to the client for full review and approval, following which procurement and manufacture commenced.
Following manufacture and successful internal testing, the client attended the Hydratron facility to carry out a factory acceptance test. The unit was put through its paces using the actual vessels, under production type conditions to ensure we had achieved the test cycle times, machine operating requirements and all the required data was being recorded correctly. The client was pleased with the results we had achieved and the finished burst test rig was installed at their manufacturing facility a short time later.
The unit has proven very effective in real-world conditions and full aftersales service and support is provided by the Hydratron team to ensure continued performance.