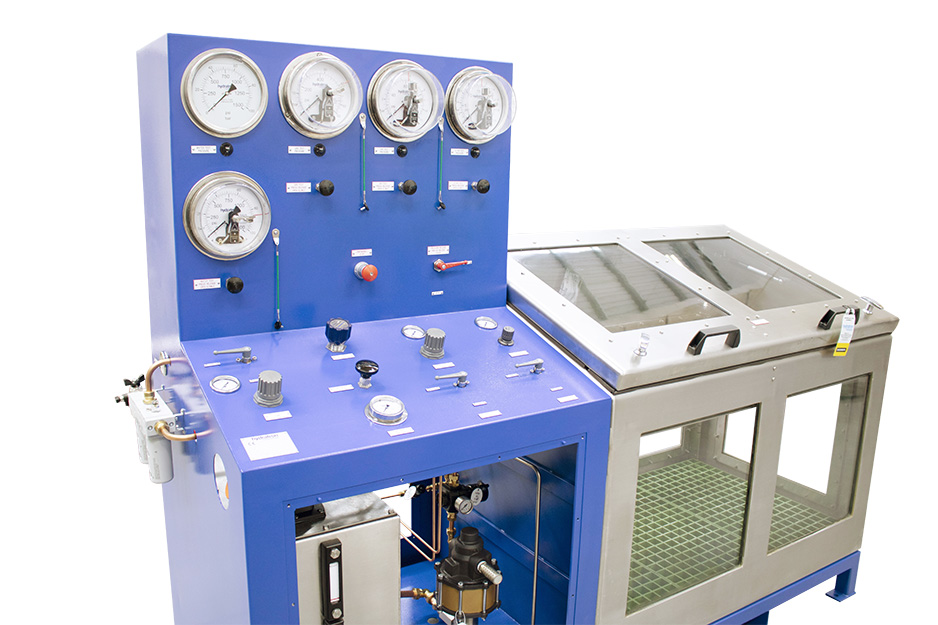
MSM aerospace fabricators, a large aerospace manufacturer, approached Hydratron with a requirement to design a pressure testing solution that could be used to test a wide range of stainless-steel aerospace components; used on various types of aircraft.
Bespoke Test Rig Requirements
The tests that were required varied from component to component but the rig had to be able to carry out hydraulic testing with pressures to 1,250PSI, gas testing with pressures to 600 PSI and low pressure air testing to 100 PSI. Submerged gas testing was also required to allow the operator to visually identify gas leak locations on the components if there was a failure.
Early in the design process a Hydratron sales engineer conducted a site visit to MSM aerospace fabricators to establish the client requirements and ascertain the technical challenges that would need to be overcome. One of the key points identified was the risks associated with gas under water testing. Operator requirements included the ability to set different limiting pressures and ensuring varying test pieces could not be over pressurised.
MSM also wanted to move away from a hand operated pump and instead use an air driven system . By doing so, operators could easily bring numerous components up to test pressure without becoming fatigued. Another design factor was that the client needed us to ensure that components did not come into contact with the stainless-steel bottom of the test compartment. This could cause damage to the test piece and prevent them from meeting the high standards required by the aerospace industry.
Key Features
- Test system allows for testing a wide variety of components in relation to: pressure, capacity, size and orientation
- Component testing with multiple methods:
including- High-pressure gas testing
- High-pressure water testing
- Low-pressure air testing
- Submerged gas testing for safe visual inspection of component leak location
- Increased safety requirements for gas under water testing
- Components can never be over pressurised
- Test components do not come into contact with test chamber walls and base
Designing the gas under water test rig
Hydraton have years of experience with gas testing of components under water using high pressure, having done many configurations of this type.
With a need to set different limiting pressures, MSM had proposed an arrangement similar to an adjustable relief valve. Our engineers raised the issue that to set and unset a relief valve for each test which would have been very time consuming. Instead we proposed a range of contact gauges that would allow the operator to limit the pressure at any set point. The operator would pre-set a pressure point on the contact gauge and once this pressure had been reached the pump would cut off, allowing the operator to check the component for leaks. This would simplify adjustment of test pressure prior to component testing.
A Hydratron AZ-1 air driven pump was integrated into the design. This removed the need for the operator to manually pump the unit up to test pressure. The Hydratron AZ-1 pumps are robust and reliable with a long service life that would withstand the volume of work this test bench would be undertaking.
Preventing non stainless to stainless contact between test piece and test compartment was achieved by using GRP grating. This acted as both a bed for the test piece to lie on as well as a means to keep the component under water when carrying out the gas testing.
Client concept approval
The proposed gas under water test rig specification was presented to MSM aerospace fabricators by our sales engineers. They walked the client through the design in detail, ensuring that they fully understood the new system and how it would work. This process also allowed the Hydratron team to confirm that we fully understood the client requirements and our bespoke test rig design had not missed anything. Once the client was fully satisfied with the design, we received the order.
Gas under water test rig – design approval & manufacture
We developed a proposed GA for client approval as final confirmation of the gas under water test rig system arrangement. Once this was approved our engineers commenced manufacture in our UK-based facility. After in-house testing and quality checks had been completed, the test rig was delivered to MSM in July 2019 and final FAT as well as product training was carried out at their facility.
Customer satisfaction
The Hydratron team worked closely with MSM in order to solve their component testing challenges and produced a bespoke testing solution. Here’s what Lee Condron, Process Manager at MSM had to say about their gas under water test rig and their interaction throughout the process with Hydratron:
“We received a new job that required pressure test to 300psi and was a difficult shape to both pressure test and also ensure visibility of all areas around the part to ensure no leakages were apparent. The current set up we currently used was both long winded and also was on the limit of the pressure test equipment. This was inadequate both from a practically basis and also there was a need to improve the health and safety of this method was being used. The overall way we were operating the pressure testing was inefficient.
I contacted Hydratron to see if they could help.
A member of there sales team came to visit and to talk about our requirements and we discussed not just this current jobs requirements but all they types of pressure testing we carried out and the different medias we were using.
We needed a pressure test unit capable of multiple tasks from gas under water to water as the media and with the accuracy required to ensure this met the demands of the drawings and customer requirements. We then discussed all the various pressure test requirements and size of components types of fitting and the requirement to hold the pieces being tested along with the requirement of the testing within the specifications required by our customers. Once developed we agreed to add some additional requirements to allow some room for potential future jobs.
Once Hydratron had a basic out line of the pressure test unit were then were invited to visit Hydratron to have a look around the factory and how the units were built and assembled and then approved through the rigorous pressure testing to prove the unit to ensure they exceeded our specification requirements and to discuss any improvements we could incorporate into the unit to ensure it supported our full range of pressure testing requirements.
Working together with the Hydratron design team we came up with a specification and design that fitted our requirements including our requirements for full viewing of the testing and quick operational change over of the rigs from one media to another along with improved fittings of adapting from one job to the next and greatly improved efficiency and safety and allowed flexibility in potential new work. Also built in the unit was a number of failsafe systems to ensure both the plant and the parts were protected from over pressurising.
Once the design was agreed Hydratron went to work on manufacture keeping us informed along the way.
We received the new unit which looked good and professional. The set up and training was given on our site and our operators were impressed with the unit’s ease of operation and safety features built into the unit all the clocks and instrumentation were clear and precise with clear indications of the setting and loading applied for each test to be carried out. Hydratron gave us all the health and safety work instruction along with all maintenance requirements required for operation so It was an easy transition to ensure the plant was up and running into production as soon as it arrived and training was completed.
We feel that the Hydratron system provided was everything we required to ensure that we had an efficient, safe pressure testing rig and this unit has excelled in providing us with this. “
To learn more about MSM, please visit their website – www.msm-aero.com (opens in new window)