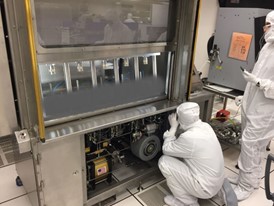
In this feature we are highlighting an upgrade we carried out for one of our global customers. Our longstanding customer had an original Hydratron gas test rig, which was supplied 20 years ago and configured for single item, manual operation only.
The purpose of the upgrade was to increase throughput and replace the original equipment with a new gas test bench equipped to perform high-pressure nitrogen testing and external helium leak testing on up to 5 devices under vacuum simultaneously. The system is installed in a class 100 (ISO5) cleanroom.
Utilised within in a production environment, as part of the final testing prior to shipment, the test bench has a fully automated touchscreen control with pre-programmed cycles to accommodate an infinite number of test variations. The digital control system means that Hydratron engineers can log into the system remotely from anywhere in the world to support their customers with troubleshooting and programming updates.
The test regime comprises of a high-pressure, nitrogen internal pressurisation cycle to identify any gross leaks or system integrity issues. This is then followed by a hard vacuum which is accompanied by an external helium spray around the test piece. Subsequently, there are helium detection measurements taken internally to ensure the product has not allowed any helium ingress, whilst under test.
The test bench comprises of the following key equipment:
- Nitrogen high-pressure test system using a Hydratron GBD double acting gas booster with electronic controls.
- Helium leak detection unit including a vacuum pump system and helium sniffing equipment.
- Test control is provided by a PC with a large and intuitive touchscreen HMI providing full control, live monitoring and recording of tests.
- Automated product work-holding system with compensated loading for a variety of product sizes and test pressures.
- Safety interlock system to prevent test pressure from being introduced into the products under test until secure clamping is detected. There is also an automatic sliding safety and viewing shield with a light curtain to ensure operator safety and that no interference can occur during the test cycle. The auto clamp circuit is interlocked with the test circuit preventing the clamps from being released until all gas pressure has been released.
All instrumentation and controls are mounted on a stainless-steel control panel situated at a convenient working height for easy operation. The equipment is assembled within a robust stainless-steel cabinet having removable panels at the front and rear for ease of maintenance.
The cabinet has been designed with ease of maintenance and manoeuvrability in mind, fork-lift truck pockets have been integrated into the underside of the cabinet to facilitate easy loading/unloading and castors to permit easy mobility. Hydratron’s engineers attended site to assist with the commissioning and Site Acceptance Testing, a provision we offer all customers, anywhere in the world.