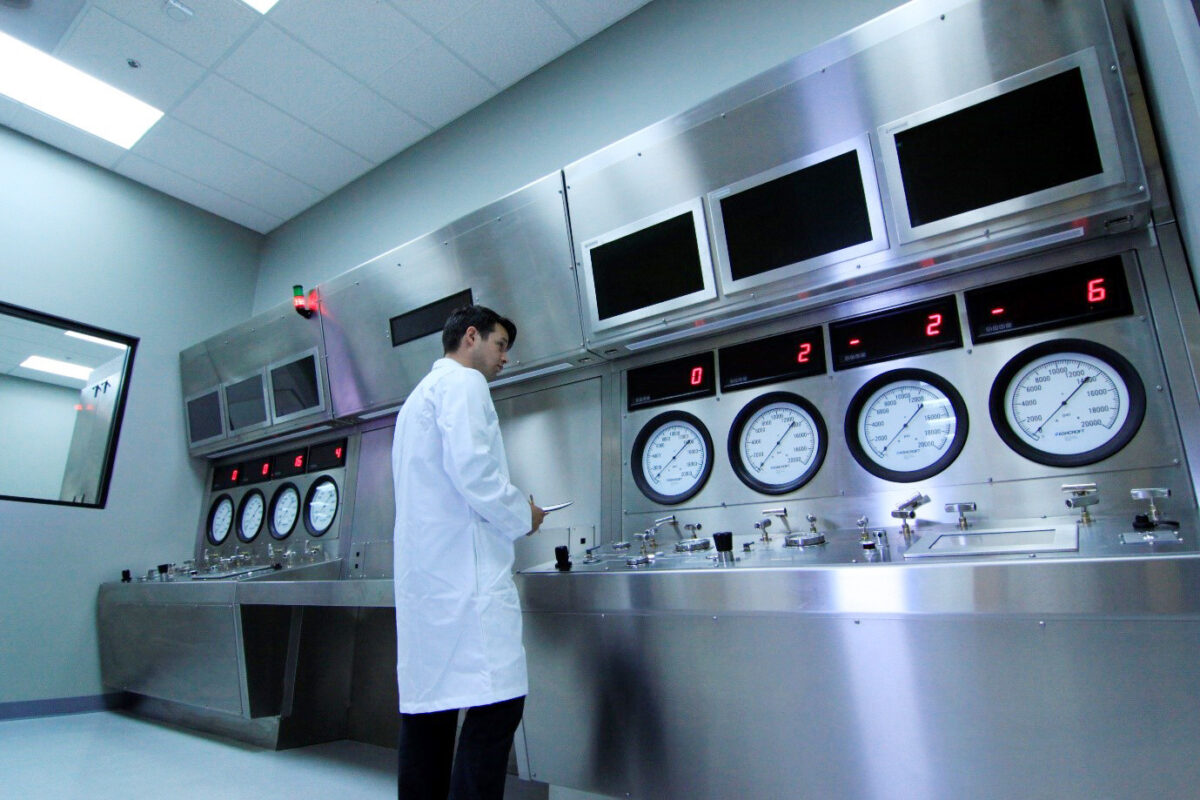
A Global Manufacturer of Subsea electrical equipment approached Hydratron asking for help in developing a “showpiece” Multi-Station Test Facility that could conduct hyperbaric pressure testing on a range of subsea products, up to 20,000psi to simulate extreme subsea pressures.
Investigation of design requirements
In common with all Hydratron projects we engaged with the operators in the company to establish the critical elements of their requirements and help guide them through the various configuration possibilities and pricing plans relating to alternative technical approaches. It became evident that whilst the testing regime required was very highly specified, the aesthetics of the pressure testing unit was equally important to them since the system would be operated in full view of staff, customers and suppliers visiting their facility. The design also needed to take into account the transportation of the test unit to the USA and had to minimise cost through design.
Following an initial visit to the customers site in North America, while it was still under construction, we proposed a number of styles that would fit well. The conclusion was that the multiple pressurisation power and control systems could be isolated away from public view, within specially designed test rooms. Highly visible operator HMI panels could be designed to embrace a bold, “larger-than-life” control room style. The entire design would be interlocking with minimal volumes for shipping and subsequent reconstruction on-site by our specialist technicians.
Key Features
- Hyperbaric testing of subsea equipment
- Pressures up to 20,000psi
- Oversized dials and displays for visual impact
- Multiple workstations
- Programmable test sequences
- Modular construction for improved logistics
- Full data logging of pressure and temperature
Technical requirements for high pressure testing
Pressure testing ranges
The multi-pump High Pressure Hydraulic Test System is suitable for hyperbaric testing at pressures up to 20,000 psi using water or mineral oil as the test medium. It is used to control the pressure cycle manually or automatically with the pressure being to be applied to the test pieces externally, within 8 independent pressure vessels.
Programmable pressurisation and depressurisation rates
When in the automatic mode, the PLC/HMI is pre-programmed to offer controlled cyclic pressurisation ramp up and depressurisation rates, in programmable stages with tight control of the rates of increase/decrease.
Customisable pressure test sequences
The PLC can store up to 100 test sequences and the ability to recall them easily. It also allows editing by the customer.
Multiple test lines and pressure indicators
Each of the eight test lines are independently controlled and dynamically displayed on the HMI touch screen. The operator can easily and accurately monitor the testing. To fulfil the requirement of making the pressure testing facility visually impressive for public viewing, each test line also displays output on an ultra-large analogue pressure gauges and ultra-large Digital Pressure Indicators.
Logging of pressure and temperature
Full data-logging is integrated within each of the test pieces to log pressure and temperature. Live data is displayed on large screens above the main control console and can be displayed and logged in both the manual and automatic modes.
Pressure testing safely
As with all Hydratron systems, safety is at the core of our design philosophy and having emergency stop buttons located on the control panel and within the test bays these activate a fail-safe shutdown, this is also linked to door interlocks and the main power supply should there be an electrical outage.
Mechanical Design
There was a lot of design effort required on the mechanical aspect of the structure. Along with the requirement to have a “wow” effect for clients coming onto their site, the test rig design needed to be modular. This allowed for the sections to packed together for shipment with the smallest possible volume (and subsequent cost to the customer) and provide the simplest possible rebuild on site. Working to very tight tolerances on the overall assembled dimensions to ensure the completed testing unit fitted exactly into the purpose constructed test control room.
Installation and commissioning the Multi-station Hyperbaric Pressure Testing Facility
Following witnessed FAT at our facility Hydratron provided a full installation and commissioning service on site and will continue to support the system integrity throughout its life.