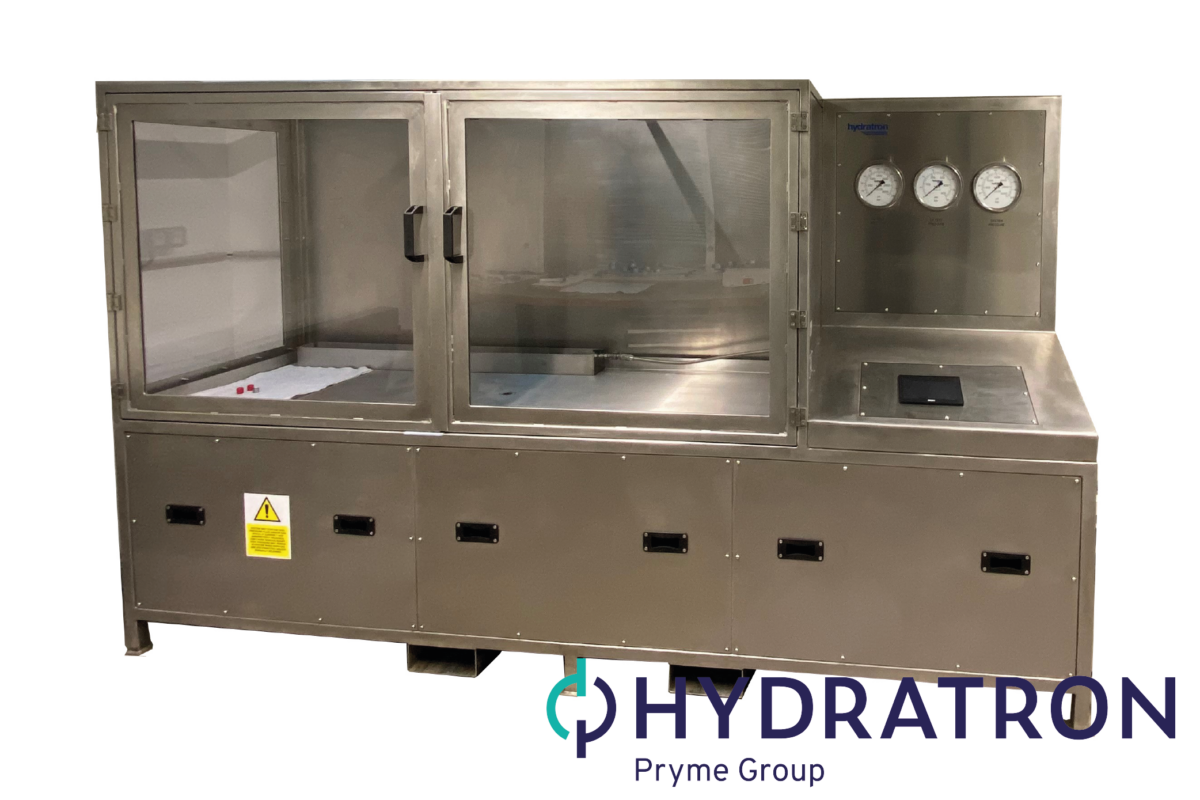
Requirement
Hydratron, a Pryme Group company, were contacted by a large aircraft company more than two years ago to discuss their onsite testing requirements in Switzerland.
After discussing their initial enquiry for a standard electric driven pump, the team identified that this option would not be suitable and designed a bespoke solution, tailored to meet the customers test and output requirements.
Initial Action
The customer required a system able to test components with water at pressures from 20psi to 2,000psi. They already had their own test manifold that would need to connect into the Hydratron test system and so an outlet bulkhead was incorporated into the design. The testing chamber needed to be large enough to house both the test manifold and the test pieces.
Automation and ease of use were also key priorities for the customer, they needed a system with the functionality to record test results and create corresponding test certificates. Furthermore, due to the range of pressures the system would be testing between, three air driven pumps were required. Smart software was written to automate the selection of the correct pump; the user enters the required pressure into the HMI and the system automatically detects which pump is required and brings the test piece up to the required test pressure for a pre-determined time period. The system then indicates whether the test piece has passed or failed and issues a certificate accordingly.
An additional consideration during the design phase was the interlocking system and steelwork on the rig, due to the size of the test compartment and the length of the doors. Due to the length of the rig, a single door would require heavy duty support – additional hinges and a support for the open door. To mitigate this, two doors were installed each with their own safety interlock whilst still enabling the user to access the test compartment easily.
The unit was delivered to the customers site in Switzerland once manufacturing and commissioning was successfully complete. User competency is critical with a system of this natures and so, remote training with the end user was conducted over Microsoft Teams to save time and save on carbon footprint. Hydratron’s service engineer will soon travel to the customers site to carry out annual servicing.